High Pressure Die Casting Machine: Revolutionizing Metal Fabrication
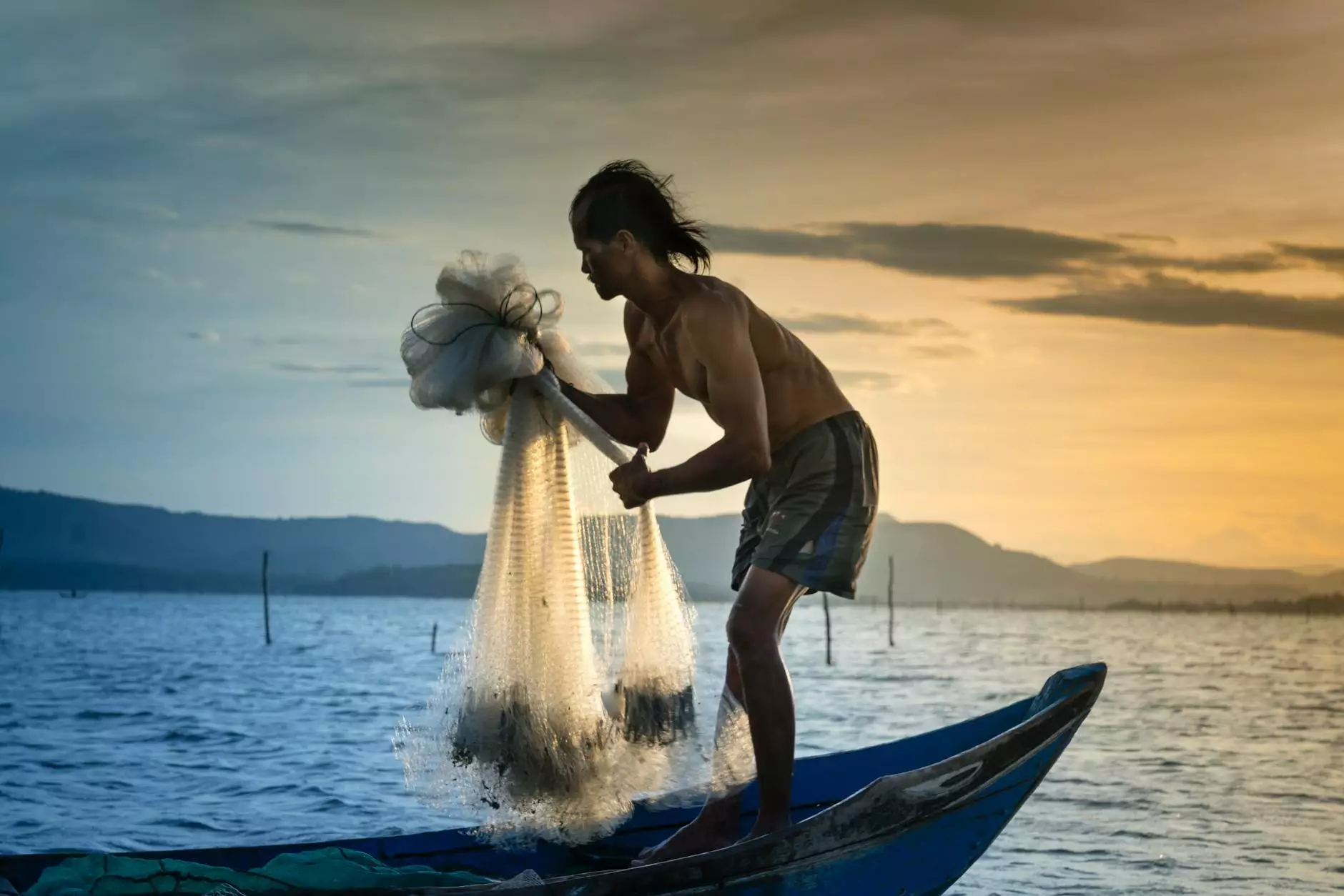
The evolution of manufacturing processes has seen significant advancements, particularly within the metal fabrication industry. One of the standout innovations in this realm is the high pressure die casting machine. This technology has transformed how metal components are produced, offering enhanced precision, efficiency, and versatility.
The Essence of High Pressure Die Casting
At its core, high pressure die casting is a manufacturing process where molten metal is forced into a mold cavity under high pressure. This process typically involves:
- Melting: Metal is melted in a furnace until it becomes a liquid.
- Injection: The molten metal is injected into the die at high velocities.
- Cooling: The metal cools and solidifies within the mold.
- Ejection: The solidified metal part is ejected from the mold.
This process allows for the production of complex geometries with high dimensional accuracy, making it suitable for various applications across different industries.
Advantages of Using High Pressure Die Casting Machines
Utilizing a high pressure die casting machine offers numerous benefits that make it a preferred choice for manufacturers:
1. Superior Surface Finish
High pressure die casting methods create parts with a smooth surface finish. This reduces the need for additional machining processes, saving time and costs. The resulting components often require minimal secondary processing, which enhances overall production efficiency.
2. Enhanced Dimensional Accuracy
Parts produced through this method exhibit excellent dimensional stability due to the nature of the die casting process. The ability to maintain tight tolerances is essential for industries where precision is paramount, such as automotive and aerospace.
3. Complex Geometries
The capability of a high pressure die casting machine to produce intricate designs is one of its major advantages. It allows manufacturers to create complex shapes that would be challenging or impossible to achieve with traditional manufacturing processes.
4. Increased Production Rates
High pressure die casting machines enable fast production cycles. As the molten metal sets quickly, manufacturers can achieve higher throughput, which is beneficial for meeting large-scale production demands.
5. Material Efficiency
The process inherently reduces material waste compared to other metal shaping methods. The precision of mold design and metal injection means that the amount of scrap generated is minimal, ultimately lowering material costs and enhancing sustainability.
Applications of High Pressure Die Casting Machines
The applications of high pressure die casting machines are diverse, reflecting their adaptability across various sectors:
1. Automotive Industry
In the automotive sector, these machines are invaluable for producing lightweight and durable components. Parts such as engine blocks, transmission housings, and structural components benefit from the strength and precision offered by die casting.
2. Aerospace Industry
For aerospace applications, weight and strength are critical. High pressure die casting machines produce components like housing parts for landing gear and other critical systems where failure is not an option.
3. Consumer Electronics
In consumer electronics, the sleek aesthetics and lightweight properties required for devices such as smartphones and laptops are achieved through die casting. The precision allows for interlocking components that fit together flawlessly.
4. Industrial Machinery
High pressure die casting is widely used in manufacturing parts for industrial machinery, where performance and durability are key. The components produced can withstand harsh operating conditions, ensuring longevity and reliability.
The Future of High Pressure Die Casting
As industries continue to evolve, so too does the technology surrounding high pressure die casting machines. Future advancements may include:
- Smart Manufacturing: Integration of IoT technologies to monitor and optimize die casting processes in real time.
- Advanced Materials: Exploration of new alloys that can withstand higher temperatures and provide better mechanical properties.
- Automation: Increased automation in die casting lines to improve efficiency and reduce labor costs.
Conclusion
The high pressure die casting machine represents a remarkable fusion of technology and manufacturing prowess. Its advantages, spanning superior surface finishes to enhanced production rates, make it indispensable in today’s competitive market. As industries leverage this technology, they are positioned to meet rising demands while ensuring quality and efficiency. The future looks bright for high pressure die casting, as it continues to play a pivotal role in shaping the future of metal fabrication.
Contact Deep Mould for Your High Pressure Die Casting Needs
If you’re considering high pressure die casting for your manufacturing needs, the experts at Deep Mould are here to help. With years of experience in the metal fabrication industry, we provide top-notch services tailored to meet your specific requirements. Visit our website at deepmould.net to learn more about our offerings and how we can assist you in achieving your production goals.